Lixel K1 is a compact handheld scanning and modeling device newly announced. With a lightweight body, it integrates 56 million-pixel panoramic vision modules and a 360° LiDAR, capable of real-time generation of centimeter-level colored 3D models. Tailored for professionals, small to medium-sized businesses, and 3D enthusiasts, it offers a convenient solution for 3D capture and modeling.
How to improve the high-temperature performance of neodymium magnets?
High temperature resistant ndfeb magnets are widely used in various applications due to their powerful magnetic properties. However, their performance tends to degrade at high temperatures, which limits their use in certain environments. The good news is that there are several methods to enhance the high-temperature resistance of these magnets, allowing them to maintain their strength and functionality in extreme conditions.
Material Composition Adjustments
One of the most effective ways to improve the high-temperature stability of neodymium magnets is by modifying their material composition. By introducing specific elements into the alloy, such as dysprosium (Dy) or terbium (Tb), the magnets can be made more resistant to heat. Dysprosium, in particular, helps to improve the coercivity (resistance to demagnetization) of neodymium magnets at elevated temperatures. This ensures that the magnet retains its strength even when exposed to extreme heat.
Coatings and Surface Treatments
In addition to altering the material composition, coatings and surface treatments play a crucial role in enhancing the high-temperature performance of durable rare earth magnets. Applying protective coatings can help shield the magnets from oxidation, which is another factor that can degrade their performance at high temperatures. These coatings provide a thermal barrier and help maintain the structural integrity of the magnet, even in harsh environments.
Advanced Magnet Design
Another approach to improving high-temperature performance is through advanced magnet design. For example, incorporating multi-layered coatings or using composite magnet structures can help distribute thermal stress more evenly. This allows the magnets to handle temperature fluctuations better without compromising their magnetic strength.
Conclusion
While neodymium magnets are known for their powerful magnetic properties, their performance at high temperatures can be a challenge. By adjusting their material composition, applying protective coatings, and optimizing their design, it is possible to significantly improve their high-temperature resistance. As technology continues to advance, these innovations will allow good performance neodymium magnets to be used in even more demanding applications, from electric vehicles to aerospace technology, where high temperature stability is critical.
suffix on a brand name | Rev.Temp.Coef.of Induction(br),a,%/℃(20-100℃) | Rev.Temp.Coef.of Coercivity(Hci),b,%/℃(20-100℃) | Maximum working temperature |
N | -0.12 | -0.6 | 80℃=176℉ |
N | -0.12 | -0.58 | 100℃=212℉ |
H | -0.11 | -0.58 | 120℃=248℉ |
SH | -0.1 | -0.55 | 150℃=302℉ |
UH | -0.09 | -0.52 | 180℃=356℉ |
EH | -0.085 | -0.5 | 200℃=392℉ |
VH/AH | -0.08 | -0.45 | 230℃=446℉ |
60℃ for N50 and N52 |
What are the challenges in processing or installing neodymium magnets?
Neodymium magnets, known for their exceptional magnetic strength, are widely used in various industries, from electronics to renewable energy. However, their mechanical properties—such as strength, brittleness, and susceptibility to damage—pose unique challenges during handling, machining, and installation. Understanding these properties is crucial for maximizing the performance and lifespan of these powerful magnets.
Neodymium Magnet Strength and Brittleness
Neodymium magnets are made from a combination of neodymium, iron, and boron (NdFeB), which gives them their remarkable magnetic properties. However, this composition also makes them inherently brittle. Unlike metals such as steel, neodymium magnets lack ductility, meaning they cannot bend or deform under stress. Instead, they are prone to chipping, cracking, or shattering when subjected to mechanical impact or improper handling. This brittleness is a result of their crystalline structure, which is optimized for magnetic performance rather than mechanical durability.
Machining Challenges
Due to their brittle nature, machining neodymium industry magnets requires specialized techniques and tools. Traditional machining methods, such as cutting or drilling, can generate excessive heat and stress, leading to cracks or fractures. To avoid this, diamond-coated tools and slow-speed machining processes are often recommended. Additionally, cooling systems are used to dissipate heat and reduce the risk of thermal damage. Even with these precautions, machining neodymium magnets remains a delicate process that demands precision and expertise.
Installation and Handling Tips
The brittleness of neodymium magnets also affects their installation and handling. Here are some best practices to minimize damage:
1. Avoid Direct Impact: Dropping or striking the magnet can cause it to crack or shatter. Always handle neodymium magnets with care.
2. Use Protective Coatings: Most neodymium magnets are coated with nickel, zinc, or epoxy to protect against corrosion and mechanical damage. Ensure the coating is intact before use.
3. Proper Tools: Use non-magnetic tools during installation to prevent sudden attraction or snapping, which can damage the magnet.
4. Temperature Control: Neodymium rare earth magnets are sensitive to temperature changes. Avoid exposing them to extreme heat, which can weaken their magnetic properties and increase brittleness.
Applications and Design Considerations
Despite their mechanical limitations, neodymium magnets are indispensable in many applications, including motors, sensors, and medical devices. To overcome their brittleness, engineers often design magnet assemblies that incorporate protective housings or support structures. For example, in high-speed motors, magnets are embedded in rotor slots to prevent centrifugal forces from causing fractures.
Conclusion
While neodymium magnets are unparalleled in magnetic strength, their mechanical properties require careful consideration during machining, handling, and installation. By understanding their brittleness and adopting best practices, users can ensure the longevity and reliability of these powerful permanent ndfeb magnets. Whether you're designing a cutting-edge motor or assembling a precision sensor, respecting the mechanical limitations of neodymium magnets is key to achieving optimal performance.
What the role of neodymium magnets in navigation technology?
High performance neodymium magnets play a crucial role in modern navigation technology, contributing to the accuracy, reliability, and efficiency of various navigational systems. As one of the strongest types of permanent magnets available, they are widely used in compasses, GPS systems, and advanced navigation technologies utilized in aerospace, marine, and automotive industries.
Enhancing Magnetic Compasses
Traditional compasses rely on Earth's magnetic field to provide directional guidance. Neodymium magnets, due to their strong and stable magnetic properties, enhance the sensitivity and durability of modern magnetic compasses. These magnets ensure higher precision and long-term reliability, making them indispensable in critical applications such as aviation and maritime navigation, where accuracy is paramount.
Supporting Inertial Navigation Systems (INS)
Inertial navigation systems (INS) rely on gyroscopes and accelerometers to determine position and movement without external references. Small powerful neodymium magnets are commonly used in high-performance gyroscopes and magnetometers, which are integral to INS. Their strong magnetic properties contribute to minimizing errors and improving the stability of navigational calculations in submarines, aircraft, and autonomous vehicles.
Advancing GPS and Satellite Navigation
Although GPS primarily relies on satellite signals, neodymium magnets play an essential role in the hardware components of GPS receivers. These magnets are used in micro-motors and actuators within satellite systems, ensuring efficient functioning of positioning and tracking equipment. Additionally, their use in sensors enhances the accuracy of GPS-based navigation, especially in remote or signal-obstructed environments.
Future Prospects in Autonomous Navigation
With the rise of autonomous vehicles, the demand for high-precision navigation systems has increased. Strong rare earth magnets are essential in LIDAR systems, motion sensors, and stabilization mechanisms, contributing to the advancement of self-driving cars and robotic navigation. Their application in these emerging technologies continues to drive innovation in navigation solutions.
In conclusion, neodymium magnets are integral to modern navigation technology, providing enhanced precision and reliability across various domains. As technological advancements continue, their role in navigation systems will only expand, shaping the future of transportation, exploration, and autonomous mobility.With ongoing innovations, the role of neodymium magnets in self-driving technology is expected to expand, further shaping the future of mobility and intelligent transportation systems.
Dynamic Torque Sensor Introduction and Features
A dynamic torque sensor is a specialized sensor used to measure and monitor torque in rotating systems. It provides real-time data on the rotational forces and enables precise control and optimization of mechanical processes. In this article, we will introduce the dynamic torque sensor and highlight its key features.
Introduction:
Dynamic torque sensors are commonly used in various industries, including automotive, aerospace, manufacturing, and robotics. They play a crucial role in measuring and analyzing torque in rotating shafts, motors, engines, and other mechanical systems. By accurately monitoring torque, these sensors help ensure efficient operation, prevent equipment damage, and enhance overall performance.
Key Features:
1 High Accuracy and Sensitivity: Rotating Torque Sensors are designed to provide highly accurate torque measurements, even in high-speed and dynamic applications. They offer excellent sensitivity to capture subtle changes in torque and allow precise adjustments in real-time.
2 Wide Measurement Range: These sensors have a broad measurement range, capable of measuring both low and high torque values. This versatility makes them suitable for a wide range of applications, from small-scale precision operations to heavy-duty industrial processes.
3 Fast Response Time: Non-contact torque sensors offer rapid response times, enabling real-time monitoring and control of torque fluctuations. Their quick response ensures timely detection of torque variations, contributing to improved safety and performance.
4 Non-Intrusive Design: Many dynamic torque sensors feature non-intrusive designs that allow for easy installation and removal without interrupting the system's operation. These non-contact sensors eliminate the need for physical contact with the rotating shaft, reducing wear and tear and minimizing maintenance requirements.
5 Robust Construction: Dynamic torque sensors are built with rugged materials and undergo extensive testing to ensure durability in demanding operating conditions. They can withstand high temperatures, vibrations, and harsh environments, ensuring reliable performance and long service life.
6 Versatile Mounting Options: These sensors offer various mounting options, including flange, shaft, or inline configurations, allowing for flexibility in installation. They can be integrated seamlessly into existing systems, making them compatible with a wide range of rotating equipment.
7 Digital Output and Integration: Many dynamic torque sensors provide digital output signals, making it easy to interface with data acquisition systems, control units, and other monitoring devices. This digital integration allows for efficient data processing, analysis, and integration into automation and control systems.
In conclusion, dynamic torque sensors play a vital role in measuring and controlling torque in rotating systems. With their high accuracy, wide measurement range, fast response time, and robust construction, these sensors enable precise monitoring and optimization of mechanical processes. Whether in automotive manufacturing, aerospace engineering, or robotics, dynamic torque sensors provide essential data for improving performance, enhancing safety, and maximizing efficiency in various industries.
EVA Rubber Technical Insights for Modern Manufacturing
Welcome to the World of Advanced Rubber Engineering
As a leading Chinese rubber supplier, Hairui Rubber understands that behind every industrial material lies a fascinating story of innovation and precision. Today, we're diving deep into the world of Ethylene-Vinyl Acetate (EVA) rubber – a material that quietly powers countless technologies around us.
Why EVA Matters in Modern Manufacturing
Imagine a material so versatile it can be found in everything from comfortable shoe soles to sophisticated electrical cables. That's EVA rubber – the unsung hero of industrial design and engineering.
Fundamental Composition Technical Insights
The Molecular Magic of EVA
For our fellow EVA foam manufacturers and engineering enthusiasts, here's a breakdown that goes beyond basic specifications:
- Vinyl Acetate Content: Precisely 45%
- Density: A robust 980 kg/m³
- Mooney Viscosity: Flexibly ranging 8-16 ML-4
Why These Numbers Matter
These aren't just random figures – they represent the engineering prowess that makes EVA a go-to solution for:
- Mechanical component design
- Advanced adhesive systems
- Specialized cable insulation
A Closer Look At Specialized Rubber Variants
Levapren Series Decoding the Codes
At Hairui Rubber, we pride ourselves on understanding the nuanced world of rubber variants:
- Levapren 452: The versatile mixer
- Complete solubility in multiple solvents
- Ideal for complex compound applications
- KA 8052: The precision specialist
- Partial solubility
- High gel content for specific industrial needs
Thermal Performance The Real-World Test
How Rubbers Survive Extreme Conditions
Let's break down how different rubbers perform under pressure:
- EPDM Rubber
- Thermal Aging Champions
- Maintains strength at 150°C
- Strategic antioxidant integration (Pb304)
- Butyl Rubber (IIR)
- More susceptible to thermal stress
- Demonstrates performance limitations
The Blending Art Industrial Alchemy
As a sophisticated Chinese rubber supplier, we understand that rubber performance is about strategic combinations:
- EPDM + NBR: Enhanced ozone resistance
- Levapren 452: Designed for optimal mixing
- Precise vulcanization rate matching
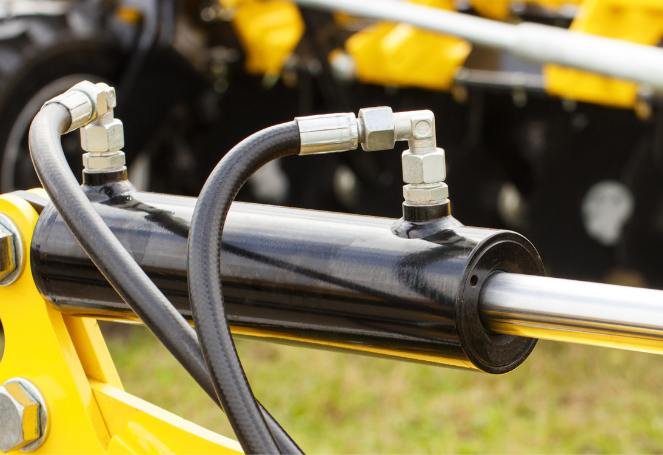
Application Domains
Industry-Specific Rubber Solutions
EVA Applications
- Cable industry insulation
- Specialized textile manufacturing
- Low-viscosity product engineering
EPDM Applications
- High-voltage cable sheaths
- Extreme weather-resistant components
Processing Considerations
Why Processing Matters
For EVA foam manufacturers, these details are crucial:
- Ash content: Minimal 1%
- Volatile components: Less than 0.7%
- Processing stability is key
Alternative Perspectives: Guayule Rubber
A unique natural alternative with:
- Biological source
- High extraction costs
- Strategic emergency resource
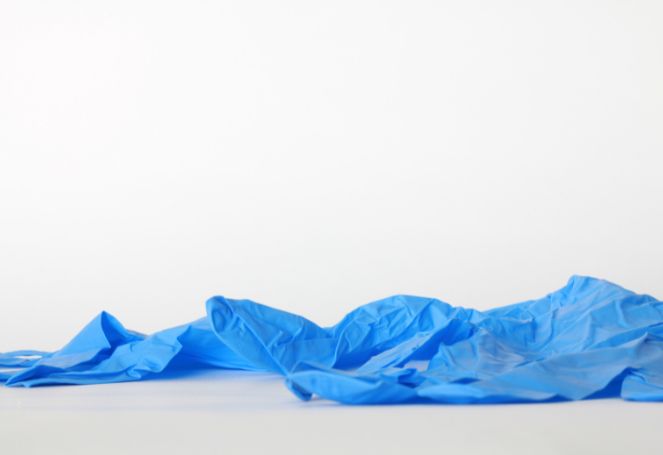
Making the Right Material Choice
Selection Framework for Engineering Professionals
Critical evaluation parameters:
- Specific operating conditions
- Material property requirements
- Environmental constraints
- Temperature tolerance
- Co-vulcanization potential
Final Thoughts on EVA Rubber Innovations
Ethylene-Vinyl Acetate (EVA) rubber represents a pinnacle of material engineering, offering exceptional versatility across industries demanding high-performance, adaptable solutions. From electrical insulation to mechanical components, EVA's unique molecular structure continues to push the boundaries of what's possible in modern manufacturing.
The true strength of EVA lies not just in its technical specifications, but in its ability to solve complex engineering challenges. While other materials may falter under extreme conditions, EVA demonstrates remarkable resilience and adaptability.
Hairui Rubber Commitment
As a leading Chinese rubber supplier, Hairui Rubber is dedicated to delivering EVA rubber solutions that meet the most demanding industrial requirements. Our expertise transforms technical challenges into innovative opportunities.
Discover the Hairui Difference – Precision. Performance. Possibility.
Check the "About Us" page to learn more about Hairui Rubber's values and services.
Why Flat Webbing Slings Are Your Ultimate Choice for Heavy-Duty Lifting Operations
When it comes to securing and lifting heavy loads, choosing the right lifting equipment is critical. One of the most trusted and versatile tools in the lifting industry is the flat webbing sling. Widely used across construction, manufacturing, and logistics sectors, flat webbing slings offer a combination of strength, flexibility, and ease of use that makes them indispensable. In this blog, we’ll explore why flat webbing slings should be your go-to choice for safe and efficient lifting operations. What Are Flat Webbing Slings Flat webbing slings are made from synthetic fibers, usually polyester, that are woven into a flat, flexible design. The simplicity of their structure combined with the strength of the material allows them to lift loads with a high level of safety and reliability. They are typically used in a variety of lifting configurations, including vertical, choked, and basket hitches, making them adaptable to almost any lifting task. High Strength-to-Weight Ratio Durability and Long Service Life Flexible and Versatile Lightweight and Easy to Handle Applications of Flat Webbing Slings Flat webbing slings are ideal for a variety of industries and applications, including: Why Choose Us for Your Flat Webbing Slings? At NANJING D.L.T SLING, LTD
Flat webbing slings are known for their impressive strength-to-weight ratio. Despite their lightweight design, they can support heavy loads, making them ideal for lifting large and bulky items. They are rated based on their lifting capacity, which can range from a few tons to over a hundred tons, ensuring you can find a sling that fits your needs.
Made from high-quality synthetic fibers, flat webbing slings are resistant to wear and tear, UV rays, and chemicals, ensuring a long service life. This durability translates into fewer replacements and reduced costs over time.
Unlike steel slings, flat webbing slings are flexible and can be easily manipulated to fit around odd-shaped or delicate loads. This flexibility allows you to lift a wide range of items with ease, while minimizing the risk of damaging the load.Safety and Protection
Safety is always a top priority in lifting operations. Flat webbing slings are designed to distribute weight evenly across the load, reducing the risk of slippage and preventing damage to both the load and surrounding structures. Additionally, they are often equipped with color-coded tags that indicate their capacity, ensuring you always choose the right sling for the job.
One of the standout features of flat webbing slings is their ease of use. They are lightweight, which makes them easy to handle, even in challenging environments. This also reduces the risk of injury to workers who may otherwise struggle with heavier lifting equipment.
Enhancing Load Handling Efficiency The Advantages of High-Quality Synthetic Fiber Slings
In today’s logistics and load handling industry, safety and efficiency are the top priorities for customers. As a leading manufacturer committed to providing high-quality lifting equipment Synthetic fiber slings are lifting tools made from high molecular fiber materials. They are widely used for hoisting, transporting, and securing heavy loads. Compared to traditional steel wire rope slings, synthetic fiber slings are lighter, more flexible, and resistant to wear, offering unparalleled advantages in improving safety and efficiency during lifting operations.What are Synthetic Fiber Slings
Nanjing D.L.T Sling, Ltd.: A Commitment to Quality and Innovation
Nanjing D.L.T Sling Your Trusted Partner for High-Quality Slings and Tie-Down Solutions
When it comes to industrial lifting, securing, and transporting heavy loads, Nanjing D.L.T Sling Co.,Ltd stands out as a reliable and trusted provider of premium slings and tie-down https://www.dlt-sling.com/products. With years of experience in manufacturing and a commitment to excellence, our https://www.dlt-sling.com/products are built to meet the highest safety standards, ensuring your operations are always secure and efficient.
Why Choose Nanjing D.L.T Sling?
At Nanjing D.L.T Sling Co.,Ltd, we understand the importance of safety, reliability, and quality. That’s why we offer a comprehensive range of https://www.dlt-sling.com/products that deliver exceptional performance under even the most demanding conditions. Here’s why our customers keep coming back:
Superior Quality and Safety
Every sling we produce is designed with safety in mind. Our slings come with a 7:1 safety factor, ensuring they exceed the safety standards needed for the toughest lifting and securing tasks. Each product is CE and GS certified, meaning they are verified for quality and compliance with international standards. You can rest assured knowing that every sling is built for maximum strength and durability.
Custom Solutions Tailored to Your Needs
We understand that no two projects are the same. That’s why we offer customized sling solutions to fit the specific needs of your business. Whether you require slings for lifting, securing, or transporting heavy equipment, we work with you to design the perfect solution that suits your load capacity, environment, and safety requirements.
Efficient Manufacturing and Quick Delivery
Our state-of-the-art manufacturing facility allows us to produce high-quality slings in large quantities without compromising on quality. We pride ourselves on our ability to meet tight deadlines and offer fast delivery to ensure that your business never experiences unnecessary delays. Whether you need a bulk order or a single custom sling, we can deliver on time and to your specifications.
Global Reach with Local Expertise
While we serve customers around the world, we understand the unique needs of different regions and industries. From construction and logistics to manufacturing and aerospace, our https://www.dlt-sling.com/products have helped businesses of all types safely lift and secure their most valuable assets. Our global presence allows us to provide localized customer service and technical support, ensuring that you always receive the best service, no matter where you are.
Our Product Range:
We offer a wide array of slings and tie-down https://www.dlt-sling.com/products to cover all your needs:
- Synthetic Fiber Slings: High-strength and lightweight, perfect for heavy-duty lifting.
- Round Slings: Ideal for delicate or irregular loads.
- High Polymer Fiber Slings: Offering superior tensile strength for high-demand applications.
- Flat Webbing Slings: Versatile and easy to use for general lifting and securing.
- Tensioners and Tie-Down Straps: Essential for securing loads during transportation.
- Custom Slings: Tailor-made solutions for your specific requirements.
Commitment to Sustainability
We believe that safety goes hand in hand with responsibility. Our https://www.dlt-sling.com/products are designed to be environmentally friendly, using sustainable materials and manufacturing processes wherever possible. As we continue to innovate, we are committed to reducing our environmental footprint while providing top-quality https://www.dlt-sling.com/products that meet the demands of a global market.
Webbing Sling The Ideal Lifting Solution for Various Industrial Needs
In the modern industrial world, the quality and safety of lifting equipment are always paramount. The webbing sling, a reliable lifting tool, stands out due to its unique design and excellent performance, making it an indispensable choice in various industries globally. Nanjing D.L.T Sling, Ltd. is dedicated to providing high-quality synthetic fiber slings to meet the lifting needs of everything from heavy machinery to precision equipment.
What is a Webbing Sling?
A webbing sling, commonly referred to as a synthetic fiber sling, is made from high-strength fiber materials woven together. Compared to traditional steel wire rope slings, they are lightweight, easy to handle, and highly flexible. Webbing slings are suitable for lifting operations of different capacities and are widely used in sectors such as construction, manufacturing, and energy. They help reduce the risk of damage to equipment during lifting and ensure operational safety.
Advantages of Webbing Sling
High Safety Factor
The main feature of a webbing sling is its safety factor, typically around 7:1. This ensures a safer lifting operation. Our products meet international safety standards and are CE and GS certified, ensuring that each sling delivers optimal safety performance during use.
Lightweight & Easy to Handle
Unlike steel wire ropes, webbing slings are much lighter, making them easier to handle. For lifting workers, this means they can complete tasks more efficiently in confined spaces.
High Strength Load Capacity
Our webbing slings have a maximum lifting capacity of up to 1100 tons, capable of handling heavy-duty equipment. Whether it’s a large machine or sensitive equipment, the webbing sling ensures stable lifting and reduces risks during the process.
Durability & Resistance to Wear
Made from high-quality polymer fibers, webbing slings have excellent abrasion resistance and tensile strength. They maintain high performance even in harsh working conditions, making them suitable for long-term, heavy-duty use.
Applications of Webbing Sling
Webbing slings are widely used in construction, mining, heavy machinery lifting, and logistics. These industries require lifting equipment that not only handles substantial loads but also operates with high safety standards and durability. Therefore, choosing a high-quality webbing sling is crucial to safeguarding worker safety and improving work efficiency.
How to Choose the Right Webbing Sling?
When selecting the right webbing sling, it is essential to consider factors such as load capacity, material, size, and the working environment. For different lifting tasks, it is important to choose a product with the appropriate safety factor. Nanjing D.L.T Sling, Ltd. offers a variety of webbing slings to meet all lifting needs. Our professional team provides tailored solutions based on the specific requirements of our clients.