The purpose of controlling the pressure difference of each clean room in a pharmaceutical factory is to ensure that when the clean room is working normally or the balance is temporarily disrupted, the air can flow from the area with high cleanliness to the area with low cleanliness, so that the cleanliness of the clean room is not disturbed by polluted air. Clean room pressure difference control is an important part of the design of the purification air conditioning system of the clean room of a pharmaceutical factory, and it is an important measure to ensure the cleanliness of the clean area. The clean room pressure difference control chapter of the "Clean Room Design Specification" GB50073-2013 (hereinafter referred to as the "Clean Specification") includes 5 contents, all of which are clauses for clean room pressure difference control. Article 16 of the "Good Manufacturing Practice for Pharmaceuticals" (revised in 2010) requires that the clean area must have a device to indicate the pressure difference.
Clean room pressure difference control is divided into 3 steps:
The first step is to determine the pressure difference of each clean room in the clean area;
The second step is to calculate the pressure difference air volume of each clean room in the clean area to maintain the pressure difference;
The third step is to take technical measures to ensure the pressure difference air volume of the clean room and maintain the constant pressure difference of the clean room.
1. Determine the pressure difference of each clean room in the clean area
According to the requirements of Article 6.2.1 and Article 6.2.2 of the "Clean Specification", a certain pressure difference must be maintained between the clean room and the surrounding space, and the positive or negative pressure difference should be maintained according to the production process requirements. The pressure difference between clean rooms of different levels and between clean areas and non-clean areas should not be less than 5 Pa, and the pressure difference between the clean area and the outdoors should not be less than 10 Pa.
① Pressure difference of each clean room in the same clean area
In actual engineering, to determine the pressure difference of each clean room in the same clean area, the pressure of each clean room can be compared with the clean area corridor, with the pressure value of the clean area corridor as the benchmark. Because the clean area corridor runs through each clean room, the pressure difference between each clean room and the clean area corridor is determined, and the pressure difference between the clean rooms is also determined. The pressure values of all clean rooms are based on the pressure value of the clean area corridor, so there will be no confusion between the pressure difference values. For example, in a solid preparation workshop, the positive pressure value of the clean area corridor can be determined to be 18 Pa (0 Pa outside the clean area); the crushing room and weighing room have serious dust dispersion, and are generally connected to the clean area corridor through the antechamber. In order to prevent the airflow with high dust content in the room from spreading to other rooms through the corridor, the positive pressure value of the crushing room and weighing room can be determined to be 12 Pa, and the positive pressure value of the antechamber can be determined to be 15 Pa. In this way, the crushing room and weighing room are at negative pressure relative to the antechamber, and the antechamber is at negative pressure relative to the clean area corridor. The airflow flows from the clean area corridor to the antechamber, and from the antechamber to the crushing room and weighing room. The clean and dry equipment storage room is used to store washed and dried equipment. To avoid contamination, the positive pressure value of the room can be determined to be 21 Pa to prevent the airflow from the corridor from flowing into the room.
② Pressure difference between clean areas of different levels
To determine the pressure difference between clean areas of different levels, you can first determine the positive pressure of the clean room with a low cleanliness level, and then increase the base of the positive pressure value in sequence to determine the positive pressure of the clean room with a high cleanliness level. For example, the water injection workshop contains a 100,000-level clean area, a 10,000-level clean area, and a partial 100-level clean area. The positive pressure value of the corridor of the 100,000-level clean area is 18 Pa, so it is necessary to increase the overall positive pressure value of the 10,000-level clean area. In short, there should be a positive pressure difference of no less than 5 Pa between the adjacent rooms of the 10,000-level clean area and the 100,000-level clean area. There are rooms in the 100-level clean area in the 100-level clean area. For this, just increase the positive pressure of the rooms in the 100-level clean area.
③ Pressure difference in clean areas in special cases
Some pharmaceutical production workshops, such as soft capsule production workshops, have clean rooms with different relative humidity in the same clean area. For this, the relatively dry clean room should be controlled to be positively pressurized relative to the adjacent clean room to prevent wet air from flowing into the dry clean room. The production plant of highly allergenic drugs such as penicillin, and clean rooms with drug powder exposure such as filling rooms should maintain a relative negative pressure.
The purpose of controlling the pressure difference of each clean room in a pharmaceutical factory is to ensure that when the clean room is working normally or the balance is temporarily disrupted, the air can flow from the area with high cleanliness to the area with low cleanliness, so that the cleanliness of the clean room is not disturbed by polluted air. Clean room pressure difference control is an important part of the design of the purification air conditioning system of the clean room of a pharmaceutical factory, and it is an important measure to ensure the cleanliness of the clean area. The clean room pressure difference control chapter of the "Clean Room Design Specification" GB50073-2001 (hereinafter referred to as the "Clean Specification") includes 5 contents, all of which are clauses for clean room pressure difference control. Article 16 of the "Good Manufacturing Practice for Pharmaceuticals" (revised in 1998) requires that the clean area must have a device to indicate the pressure difference.
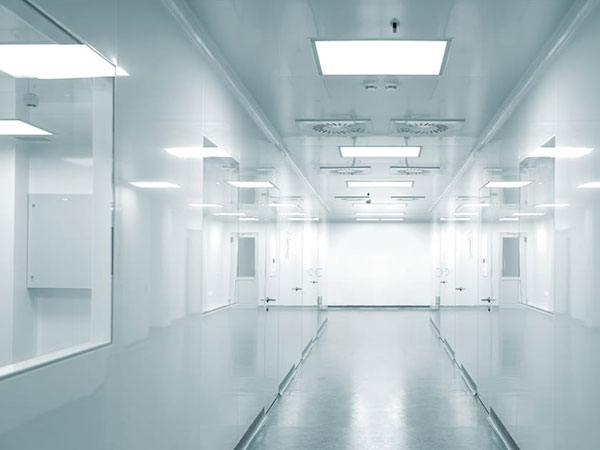
2. Determine the pressure differential air volume to maintain the pressure difference
The pressure differential air volume to maintain the positive pressure difference in each clean room in the clean area needs to be supplemented by outdoor fresh air. Therefore, the size of the positive pressure differential air volume in the clean room directly affects the fresh air ratio of the purification air conditioning system and the energy consumption of the purification air conditioning system. The pressure differential air volume to maintain the negative pressure difference in each clean room in the clean area penetrates into the clean room from the outside of the clean room. In many cases, it is the outdoor air that has not been purified. Therefore, the size of the negative pressure differential air volume in the clean room is directly related to the cleanliness of the negative pressure clean room. At present, the common methods for calculating the pressure differential air volume in the clean room are the gap method and the ventilation number method. The gap method is to estimate the pressure differential air volume of the clean room based on the total length of the gaps such as doors and windows in the clean room. However, in actual applications, the work of counting the number of gaps such as doors and windows is relatively cumbersome and prone to errors and omissions, and is currently less used. The ventilation number method is to estimate the pressure differential air volume of the clean room based on the number of ventilation times in the clean room. In actual engineering applications, this method has the advantages of simplicity, ease of operation, and high accuracy, and is a commonly used method. Article 6.2.3 of the Clean Specifications recommends the ventilation frequency method and proposes to select according to the following data: 1 to 2 times/hour when the pressure difference is 5 Pa, 2 to 4 times/hour when the pressure difference is 10 Pa. Other reference books also have recommended values, such as the Practical Heating and Air Conditioning Design Manual (hereinafter referred to as the Manual), which recommends 0.7 times/hour when the pressure difference is 4.9 Pa, and 1.2 times/hour when the pressure difference is 9.81 Pa. However, in actual applications, people have found that the data recommended by the Clean Specifications tend to be conservative, consume a large amount of pressure difference air volume, and are not economical; while the values recommended by the Manual are more appropriate. In actual projects, it is entirely possible to reduce the pressure difference air volume in the room by strengthening the air tightness of the clean room enclosure structure. According to the size of the pressure difference value of the clean room, the pressure difference should be selected according to the ventilation frequency of 1 to 2 times/hour.
The purpose of controlling the pressure difference of each clean room in a pharmaceutical factory is to ensure that when the clean room is working normally or the balance is temporarily disrupted, the air can flow from the area with high cleanliness to the area with low cleanliness, so that the cleanliness of the clean room is not disturbed by polluted air. Clean room pressure difference control is an important part of the design of the purification air conditioning system of the clean room of a pharmaceutical factory, and it is an important measure to ensure the cleanliness of the clean area. The clean room pressure difference control chapter of the "Clean Room Design Specification" GB50073-2001 (hereinafter referred to as the "Clean Specification") includes 5 contents, all of which are clauses for clean room pressure difference control. Article 16 of the "Good Manufacturing Practice for Pharmaceuticals" (revised in 1998) requires that the clean area must have a device to indicate the pressure difference.
3. Maintain constant pressure difference in clean rooms
The above-mentioned pressure difference value and pressure difference air volume in clean rooms are only theoretical values, which need to be realized by certain technical measures and facilities. In actual projects, there are many ways to control the pressure difference in clean rooms:
Under normal circumstances, there are many ways to adopt a constant air volume system, that is, first ensure that the clean room air supply volume is relatively constant, adjust the clean room return air volume or exhaust air volume, so as to control the clean room pressure difference air volume and maintain the clean room pressure difference value; you can also install a manual split multi-leaf regulating valve or butterfly valve on the clean room return (exhaust) air branch pipe to adjust the return (exhaust) air volume and control the indoor pressure difference. Its advantages are simple equipment and effectiveness.
The method of adjusting the pressure difference in the clean room during the commissioning of the air conditioning system has the disadvantage that when the pressure difference in the clean room deviates from the set value during the operation of the air conditioning system, it is more troublesome to adjust. This method is used in conjunction with other methods and is one of the common means of controlling the pressure difference in clean rooms in current projects.
Installing a damping layer (such as a single-layer non-woven fabric, stainless steel filter, aluminum alloy filter, nylon filter, etc.) at the return (exhaust) air outlet of the clean room can effectively ensure the positive pressure of the clean room, but the filter as the damping layer needs to be replaced frequently to prevent the positive pressure in the clean room from being too high.
Install a residual pressure valve on the partition wall of the adjacent room to control the positive pressure. Its advantages are simple and reliable equipment, and its disadvantages are that the residual pressure valve is relatively large in size, the ventilation volume is limited, it is not convenient to install, and it is not convenient to connect with the air duct, and it can only be installed in individual clean rooms.
Install an electric actuator system on the valve shaft of the return (exhaust) air branch regulating valve in the clean room, so as to form an electric regulating valve with the corresponding valve. According to the feedback of the clean room pressure difference value, fine-tune the valve opening, and automatically adjust the pressure difference in the clean room to return to the set value. This method is used to control the pressure difference in the clean room more reliably and accurately, and the control system cost is not high. It is widely used in engineering practice. The system can be installed on the return (exhaust) air branch regulating valve of the clean room or the typical clean room that needs to display the pressure difference.
Install Venturi air volume control valves on the air supply branch and return (exhaust) branch in the clean room. There are three types of Venturi valves: fixed air volume valves, which can provide stable air flow; bistable valves, which can provide two different air flow rates, namely maximum and minimum flow rates; variable air volume valves, which can control the air flow rate through closed-loop response to instructions and flow feedback signals in less than 1 second. Venturi valves are not affected by changes in duct pressure, have rapid responses (less than 1 second), and are precisely adjusted, but the equipment is relatively expensive and is suitable for use in some biological product production plants that require negative pressure control, toxic and biosafety laboratories (such as P3 biological laboratories), and other places. Because personal safety issues must be considered, the system pressure differential control must be high-precision and highly reliable. In this regard, by using constant air volume valves and bistable valves, the supply and exhaust air volumes of the clean room (or laboratory) can be strictly controlled, thereby forming a stable pressure differential air volume and controlling the pressure differential of the clean room (or laboratory) to be stable; using variable air volume valves to regulate the room so that the flow rate of the supply air duct valve tracks the flow rate of the exhaust air duct valve, a stable pressure differential air volume can be formed and the pressure differential of the clean room (or laboratory) can be controlled to be stable.